Equipment for handling materials encompasses any device or tool utilized for moving, processing, storing, or packaging various materials. This includes items such as forklifts, conveyor systems, shelving units, and even self-governing mobile robots (AMRs).
Employing this type of equipment enhances efficiency and can automate tasks traditionally done by hand, leading to time and cost savings. Material handling equipment is frequently used in scenarios like processing grains in agriculture, managing and storing items in warehouses, and handling the loading and unloading of materials like soil or landscaping elements.
Four Primary Types of Material Handling Equipment
There are four principal types of material handling equipment: storage and handling devices, industrial vehicles, equipment for handling bulk materials, and engineered systems.
Here’s a breakdown of typical applications and tools for each category:
Storage and Handling Devices
This category is the most fundamental. It involves equipment used for holding products as inventory or materials waiting for the next stage in production. These tools are crucial for optimizing space usage, especially in terms of vertical and floor space.
Typical storage devices include:
- Bins and Drawers:
Suitable for small to medium items, bins have open tops for easy access, while drawers offer dense storage, often more space-efficient than shelving. - Mezzanines:
Semi-permanent structures that create an additional level between the floor and ceiling, expanding the usable area of a warehouse. - Pallets: Designed for storing packaged loads, facilitating their movement and transportation with industrial trucks or pallet jacks.
- Pallet Stacking Frames: Attachable to pallets, these frames enable stacking of palletized loads and are space-efficient when not in use.
- Storage Containers: Also known as shipping containers, they vary in size and are ideal for storing large items or quantities.
- Storage Racks: Like shelves, these racks or pallet racks utilize vertical space with multiple horizontal platforms. Drive-in racks increase storage capacity but may reduce accessibility.
Industrial Trucks and Machines
These are employed for loading and transporting materials and can range from manually operated hand trucks to motorized forklifts. Industrial trucks are often equipped with fork attachments, making them suitable for handling palletized loads.
Frequently Used Industrial Trucks in Material Handling:
- Forklifts: Standard models in warehouses typically lift loads up to 5,000 pounds and reach heights of 10 to 15 feet. There are also larger variants for heavier loads.
- Order Pickers: These elevate warehouse workers to retrieve items from high shelves. They usually have a capacity of around 3,000 pounds and can extend up to 32 feet.
- Pallet Jacks: Known also as pallet trucks, these are available in manual and electric forms. They generally move one to two pallets at a time, with a maximum load capacity of about 5,500 pounds for standard models, though higher-capacity models exist.
- Side Loaders: A variation of forklifts, these have side-mounted forks, enabling them to operate in narrow aisles and load items without rotating the cab.
- Walkie Stackers: These are operated from behind rather than from a cab. They resemble pallet jacks in load capacity, ranging from 2,000 to 4,000 pounds, and can lift between 5 to 10 feet.
Equipment for Handling Bulk Materials
This type of equipment is designed to transport, load, and process large volumes of materials, ranging from small items like grains or stones to larger goods like packaged consumer products.
Such equipment is versatile, being used in both indoor and outdoor settings. For instance, silos might be used on farms for storing bulk food items, while conveyors in warehouses facilitate the movement of packages.
Widely Used Bulk Material Handling Equipment:
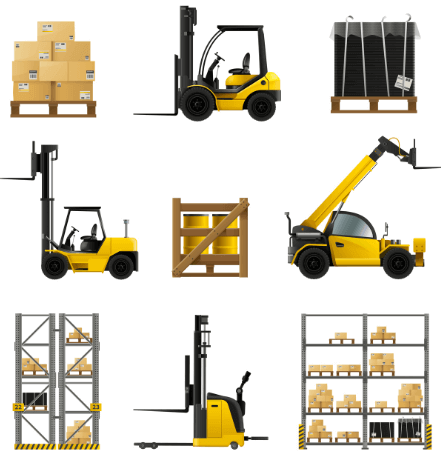
- High Viscosity: Grease lubrication is characterized by a higher viscosity compared to its liquid counterparts. This attribute allows it to create an effective protective film between surfaces, ensuring continuous lubrication and significantly reducing friction, heat, and wear.
- Bucket Elevators: Also known as grain legs, these are used for vertically transporting flowable bulk materials, commonly in agricultural settings for moving materials like grain or fertilizer.
- Exceptional Adhesion: The ability of grease to adhere to metal surfaces is a notable feature. This adhesion ensures that the grease remains in place, effectively resisting displacement caused by vibration, shock, or centrifugal forces. Such a quality renders grease lubrication particularly suitable for scenarios where oil leakage poses a significant concern.
- Conveyors: These systems facilitate the movement and processing of materials in bulk, functioning like traditional assembly lines with belts and pulleys to transfer items from one point to another.
- Inserting image…Bulk-Handling Cranes: An advanced version of standard cranes, these are equipped with a two-piece hinged grab for lifting and balancing bulk cargo such as coal or mineral ore.
- Dump Trucks: Specialized vehicles for transporting and unloading large quantities of materials, commonly used in construction for removing debris or carrying loose materials.
- Hoppers: Typically found in agricultural contexts, hoppers are containers for bulk products like grain and corn, featuring bottom compartments for unloading.
- Stackers and Reclaimers: Stackers accumulate bulk materials like ore or coal, while reclaimers then load these materials, often transferring them to a conveyor for movement.
- Silos: Tall, cylindrical structures used for storing high volumes of items like coal, woodchips, or animal feed.
Engineered Systems
Engineered systems are fully automated setups designed to reduce manual labor. These are prevalent in manufacturing and warehousing environments.
Key engineered systems include:
- Automated Storage and Retrieval Systems (AR/RS): Robotic systems capable of storing and retrieving materials from designated locations.
- Automated Guided Vehicles (AGV): Also known as self-guided vehicles, AGVs operate autonomously, following specific paths or navigational aids.
- Autonomous Mobile Robots (AMRs): More sophisticated than AGVs, AMRs navigate using sensors to map and adapt to their environment.
- Palletizers: Machines that automate the process of stacking items on pallets, subsequently moving the pallets onto conveyors.
- Sortation Systems: Systems that automatically identify objects and sort them to designated locations.
- Warehouse Robots: AI-driven robots tailored for warehouse tasks, automating repetitive activities like product retrieval.
Selecting the Right Material Handling Equipment
The choice of material handling equipment hinges on various factors, including the nature of the manufacturing, warehousing, agricultural, or construction tasks.
Considerations for Selection:
- Function and Space: Aim for efficiency in utilizing space. For instance, a tier might expand the usable area in a warehouse.
- Material Types: The size and nature of the materials dictate the equipment needed. For example, granular items might require packaging, while boxed items are more easily palletized.
- Environment: Outdoor tasks might necessitate cranes for moving large items or reclaimers for sorting through piles.
- Automation vs. Labor: While automation enhances efficiency, it also incurs costs. A blend of automated and manual equipment is often optimal, such as using robotic systems for initial picking in a warehouse, followed by human involvement for quality checks and packaging.
If you are looking forward to investing in qualitative materials handling equipment, please feel free to contact us and we will get you the best solution at KG International.