Roller bearings are indispensable in the world of machinery and industrial operations. These components support rotational and axial movements while minimizing friction, which is crucial for enhancing the efficiency and longevity of any mechanical system. This blog aims to provide information about the fundamentals of roller bearing types, including their design, and applications, and provide insights on selecting the most appropriate kind for your specific engineering requirements.
Understanding Roller Bearings
Roller bearings are integral components in the functionality of various machines, playing a pivotal role by facilitating smoother operations and significantly reducing wear and tear on moving parts. These bearings are designed to support substantial loads while allowing rotation or linear movements with minimal friction. The profound reduction in friction enhances the operational efficiency of machinery and extends its lifespan. This makes roller bearings an indispensable element in numerous mechanical setups. By ensuring that parts move smoothly and efficiently, roller bearings contribute to the overall reliability and performance of the equipment, proving vital in a wide array of industrial applications.
Comprehensive Overview of Roller Bearing Types
The classification of roller bearings can be detailed, as they are designed to meet specific needs in various applications. Here is a closer look at some of the common types:
Cylindrical Roller Bearings
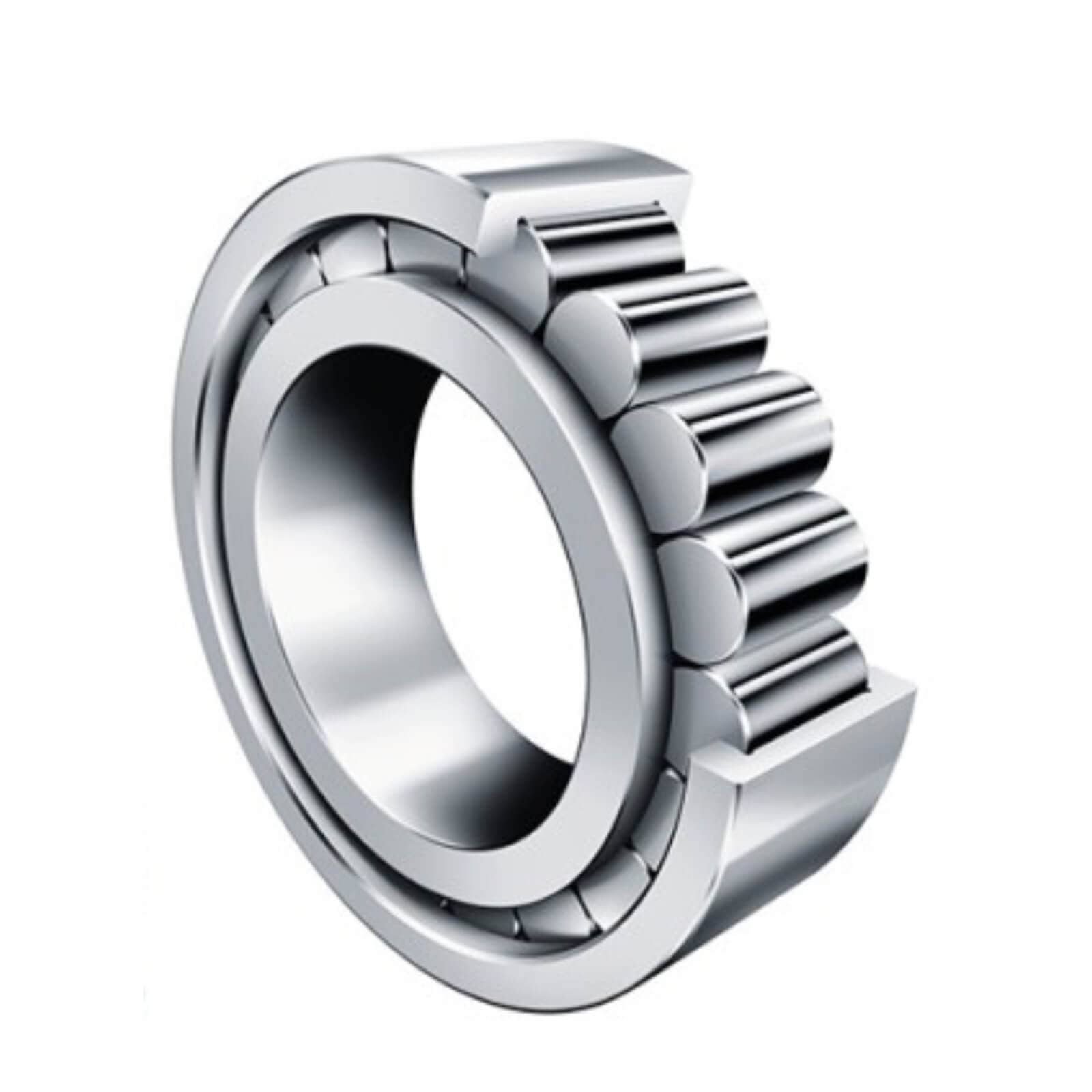
These bearings are engineered to manage high radial loads and operate effectively at moderate speeds. They utilize cylindrical rollers as the rolling elements, which spread the load over a larger surface area, providing more support and reducing deformation under heavy loads.
- Single Row Cylindrical Roller Bearings: These are suitable for high-speed applications and can handle radial loads efficiently. Their design allows for some axial displacement of the shaft relative to the housing.
- Double Row Cylindrical Roller Bearings: These are excellent for applications requiring high radial rigidity and can handle heavier loads than their single-row counterparts.
Spherical Roller Bearings
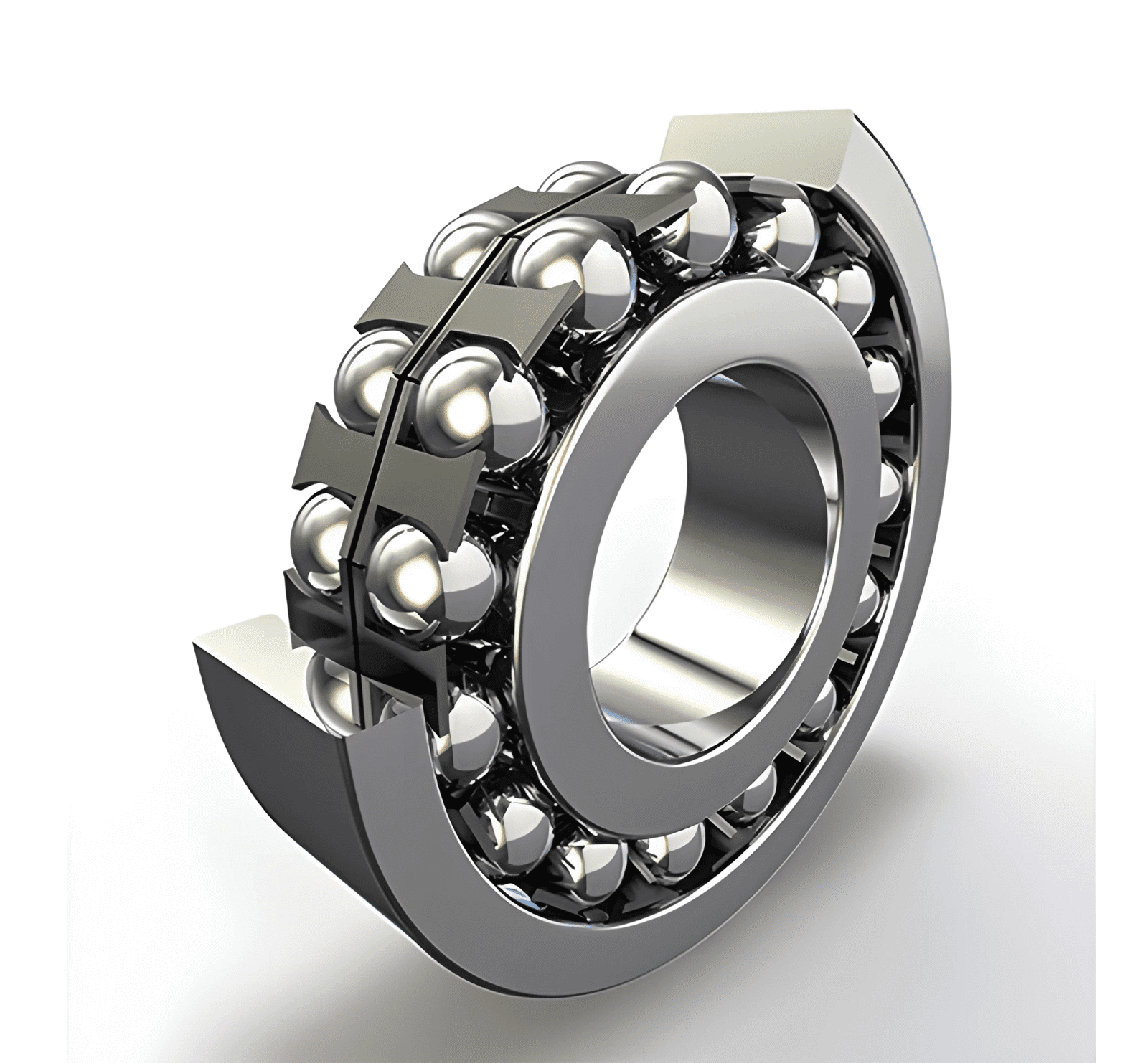
Spherical roller bearings are ideal for applications involving misaligned or deflected shafts. The spherical shape of the outer ring allows the bearing to accommodate angular misalignment, commonly caused by mounting or shaft deflection errors.
Needle Roller Bearings
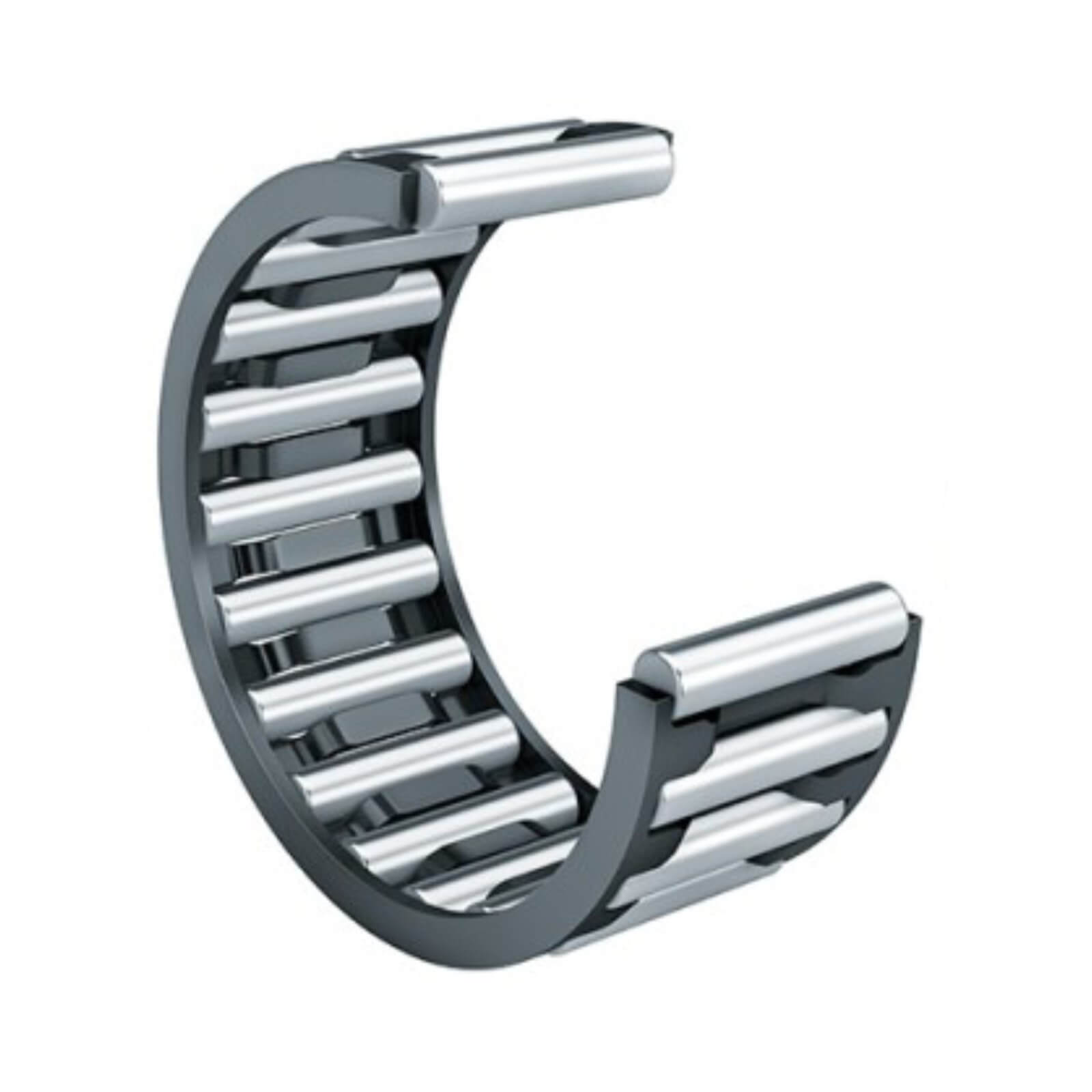
Needle roller bearings are designed for applications where space is limited but high load capacity is required. These bearings feature long, slender rollers, enabling them to fit into compact spaces while maintaining optimal performance.
Taper Roller Bearings
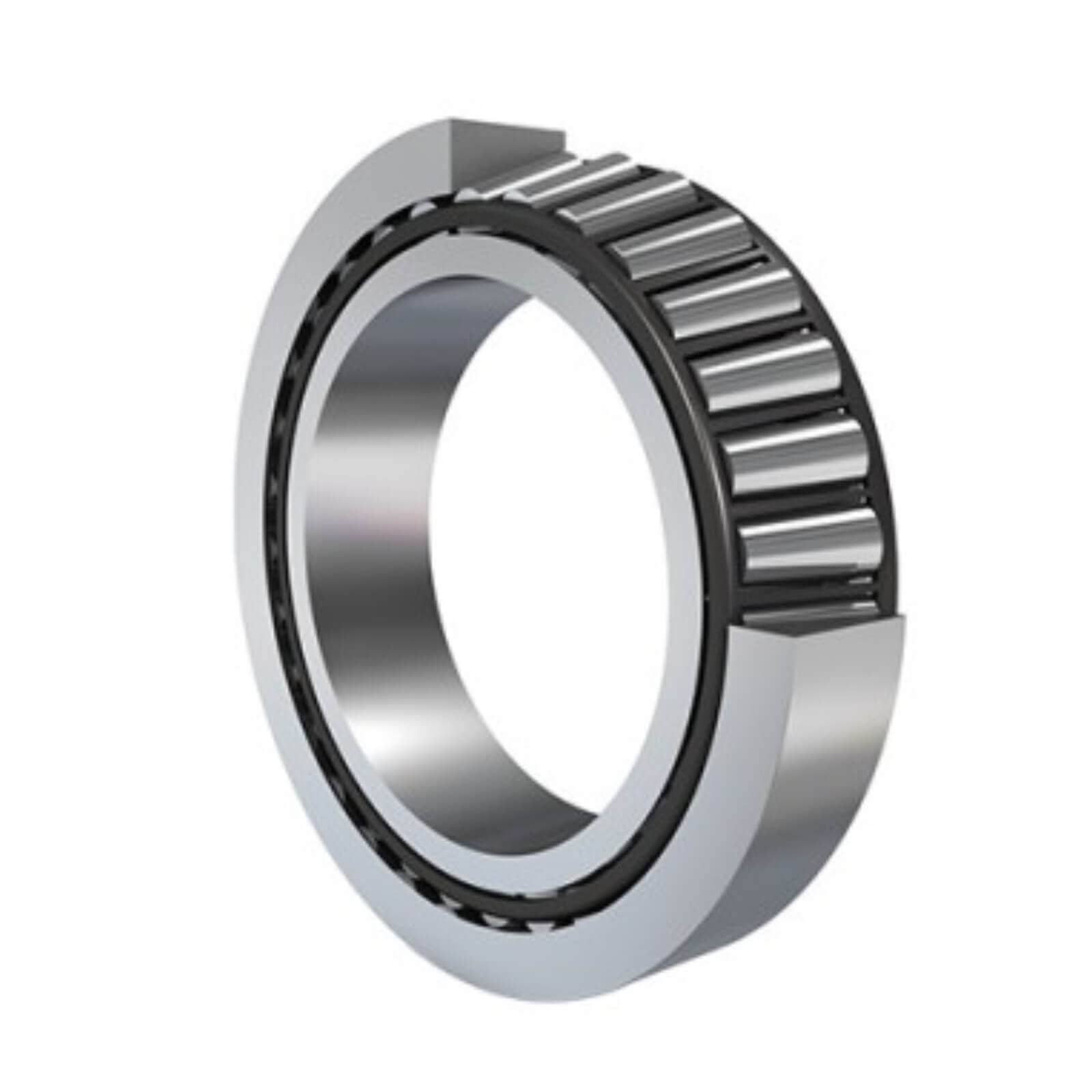
Taper roller bearings are designed to handle radial and axial loads. The taper angles allow the bearings to hold a more significant amount of radial load and thrust load in one direction. These are commonly used in automotive wheel hubs.
Applications Across Various Industries
Roller bearings are versatile and can be found in a variety of applications across different sectors:
- Automotive: They are used in almost every mechanical component of a vehicle, including transmissions, clutches, pumps, and wheel bearing arrangements.
- Industrial Machinery: Roller bearings are essential in rotating parts of heavy machinery, helping to maintain precision and efficiency in harsh industrial environments.
- Medical Equipment: High precision and reliability are critical in medical applications, and roller bearings are used in devices like MRI machines, where high speed and low noise are necessary.
- Household Appliances: In appliances such as washing machines and air conditioners, roller bearings help ensure reliability and enhance energy efficiency.
- Agriculture: Durable and robust roller bearings are used in agricultural machinery to withstand harsh conditions and heavy loads.
Anatomy of a Roller Bearing
Understanding the components that make up a roller bearing can help in selecting the right type for your needs:
Component | Description |
---|---|
The Outer Race | The exterior ring that holds the bearing assembly, typically mounted within the housing. |
The Inner Race | Attached to the rotating part of the shaft, this component is crucial for the smooth operation of the bearing. |
The Rollers | Load-bearing components that roll between the inner and outer races, carrying the mechanical load. |
The Cage | Maintains the rollers in even spacing and alignment, preventing contact and friction between them. |
The Seal | Protects the bearing from external debris and contaminants, enhancing durability and performance. |
Selecting the Right Roller Bearing Type
To select the appropriate roller bearing for your application, consider the following steps:
- Load Type and Magnitude: Determine the precise nature of the load (whether radial, axial, or a combination of both) and its magnitude to ensure the chosen bearing can effectively handle the expected stress.
- Operational Speed: Evaluate the speed requirements of your application thoroughly and ensure the selected bearing can accommodate it without the risk of overheating or suffering from excessive wear and tear over time.
- Application Conditions: Consider environmental factors such as temperature extremes, the presence of contaminants, or the potential for corrosion, which could impact the performance and durability of the bearing.
- Space Limitations: Ensure the chosen bearing fits perfectly within the space available in your machinery, considering both physical dimensions and the installation requirements for optimal performance.
Leveraging KG International’s Expertise
KG International excels in bearing technology, offering an extensive selection of roller bearing types crafted to address the diverse requirements of industries worldwide. Our commitment to excellence is evident in every bearing we produce, each rigorously tested to meet stringent quality standards. We ensure that our products consistently deliver superior results by focusing on reliability and performance. With decades of experience and a deep understanding of industry requirements, KG International is dedicated to achieving customer satisfaction through innovation, quality, and comprehensive product selection. Trust us to enhance the operational efficiency of your machinery with our expertly engineered solutions.
Conclusion
Understanding the various roller bearing types, their components, and specific applications empowers you to make well-informed decisions tailored to your engineering requirements. Whether you need roller bearings for heavy industrial equipment, precision medical instruments, or robust agricultural machines, choosing the right type cannot be overstated. KG International stands ready to assist you in this selection process, offering a comprehensive array of roller bearings designed for optimal performance and reliability. Our expertise and commitment to quality ensure that you receive the best solutions for your needs, making us a reliable partner in your quest for mechanical excellence.