Do you hear that squeaking sound? Or feel that unusual vibration? It could signal trouble with the bearings of your machinery. Choosing the right bearings is only half the battle. Proper installation, maintenance, and understanding the application are crucial for optimal performance and longevity. This guide shows you how to ensure you are making the right use of bearing and avoid costly downtime.
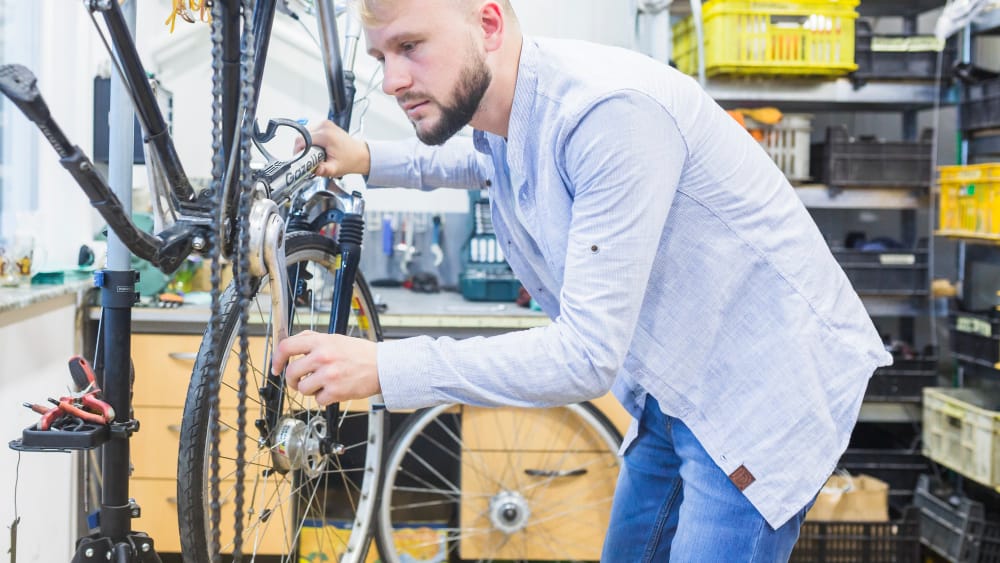
This blog will cover essential aspects from selection to troubleshooting, guaranteeing your bearings deliver peak efficiency. KG International, a leading supplier of bearings, understands the importance of correct bearing implementation. Let us guide you.
Why Correct Use of Bearing Matters
Bearings are essential components in countless machines. They reduce friction and enable smooth movement. Poor use of bearing leads to:
- Premature failure
- Reduced efficiency
- Increased energy consumption
- Costly repairs and replacements
- Unplanned downtime
Investing in proper bearing practices yields substantial returns. You will see improved machine performance and a longer lifespan.
Selecting the Right Bearings for the Job
Choosing the correct type is the initial and vital step in ensuring proper use of bearings. Consider these factors:
- Load: Determine the radial and thrust loads the bearing will endure. Different bearing types excel under different load conditions. Ball bearings handle lighter loads and high speeds while roller bearings are best for heavier loads.
- Speed: Analyze the operating speed as high-speed applications need bearings with appropriate lubrication and tolerances.
- Environment: Think about the operating environment. Temperature, contaminants, and corrosive substances affect bearing choice. Sealed bearings or specific materials might be necessary.
- Space constraints: Evaluate the available space. Different bearing types have different dimensions. Needle bearings, for example, are useful when radial space is limited.
- Precision: Consider the required level of precision. Precision bearings provide higher accuracy and tighter tolerances.
Refer to bearing catalogs and consult with experts like KG International to pinpoint the optimal bearings for your specific application.
Proper Installation Techniques
Even the best bearing will fail if installed incorrectly. Adhere to these best practices:
- Cleanliness: Ensure the work area, tools, and bearing are free of contaminants. Dirt and debris cause premature wear.
- Proper Tools: Use correct tools for mounting and dismounting bearings. Avoid using hammers directly on the bearing. Bearing pullers and presses provide controlled force.
- Correct Fit: Verify the shaft and housing dimensions match the bearing specifications. Interference fits are often required.
- Alignment: Ensure proper shaft alignment. Misalignment puts undue stress on the bearing.
- Lubrication: Apply the correct type and amount of lubricant during installation.
Always consult the manufacturer’s instructions for specific installation guidelines.
Lubrication: The Lifeline of Bearings
Proper lubrication is vital for extending bearing life and maximizing the benefit from the use of bearings.
- Choose the right lubricant: Consider the operating temperature, speed, and load. Grease is common for general applications while oil lubrication is suitable for high-speed or high-temperature environments.
- Apply the correct amount: Too little lubricant leads to friction and wear. Too much lubricant causes heat buildup. Hence, follow the manufacturer’s recommendations.
- Relubricate at proper intervals: Relubrication frequency depends on the application and lubricant type. Therefore, establish a maintenance schedule.
- Prevent contamination: Use clean grease guns and oil dispensers or automated lubrication. Seal bearing housings to prevent dirt and moisture from entering.
Regular lubrication prevents metal-to-metal contact and dissipates heat. This ensures smooth operation and prolonged bearing life.
Condition Monitoring and Maintenance
Regular condition monitoring identifies potential problems before they escalate.
- Vibration Analysis: Detects defects in bearings early and changes in vibration patterns indicate wear or damage.
- Temperature Monitoring: High bearing temperatures signal excessive friction or inadequate lubrication.
- Visual Inspection: Check for signs of damage, lubricant leaks, or corrosion.
- Oil Analysis: Assess the condition of the lubricant and identify wear particles.
Implement a proactive maintenance program based on these techniques. Addressing issues early prevents catastrophic failures.
Troubleshooting Common Bearing Problems
Even with proper care, bearing problems can occur. Here are some common issues and their possible causes:
- Excessive Noise: Could indicate contamination, damage, or improper lubrication.
- High Temperature: Might result from over-lubrication, under-lubrication, or excessive load.
- Vibration: Often caused by misalignment, imbalance, or bearing defects.
- Premature Failure: Usually results from incorrect bearing selection, improper installation, inadequate lubrication, or contamination.
Thoroughly investigate any abnormal symptoms to identify and resolve the root cause.
Conclusion: Optimizing the Use of Bearings for Peak Performance
Mastering the use of bearings leads to significant improvements in machine reliability and efficiency. From initial selection to ongoing maintenance, every step matters. By following the best practices outlined in this guide, you can maximize bearing life, minimize downtime, and ensure optimal performance.
Contact KG International today to explore a wide selection of high-quality bearings and expert support. Let KG help you optimize your bearing applications for long-term success. Visit the website at www.kginternational.com