When it comes to selecting the right bearings for your machinery, understanding the distinct characteristics of Angular Contact Ball Bearings and Roller Bearings is crucial. Each type offers unique benefits and is suited to different applications. This detailed comparison will guide you in choosing the most appropriate bearings for your project needs.
Angular Contact Ball Bearings
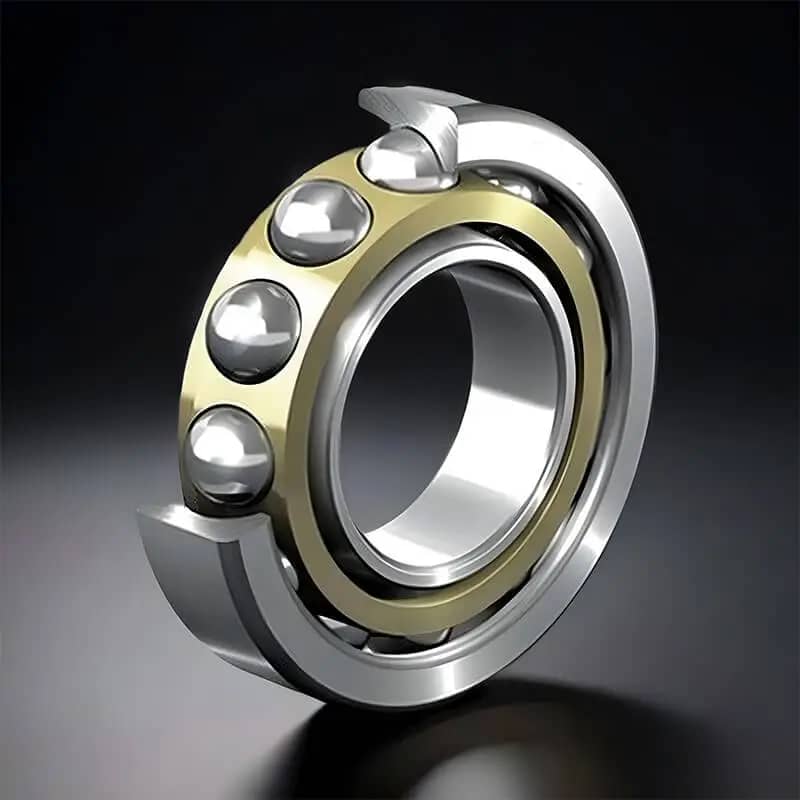
Usage and Applications: Angular Contact Ball Bearings are designed to withstand combined loads, handling both radial and axial forces simultaneously. Their unique design allows them to operate at high speeds while maintaining precision and reducing friction. Common applications include:
- High-speed spindles in drilling machines
- Precision milling machines
- Gearboxes
- Pumps and compressors
Benefits of Angular Contact Ball Bearings
High Load Capacity: These bearings can support significant loads due to their angular contact design.
Precision: They maintain high precision and rigidity under high-speed conditions.
Speed: Capable of operating at higher speeds compared to many roller bearings.
Roller Bearings
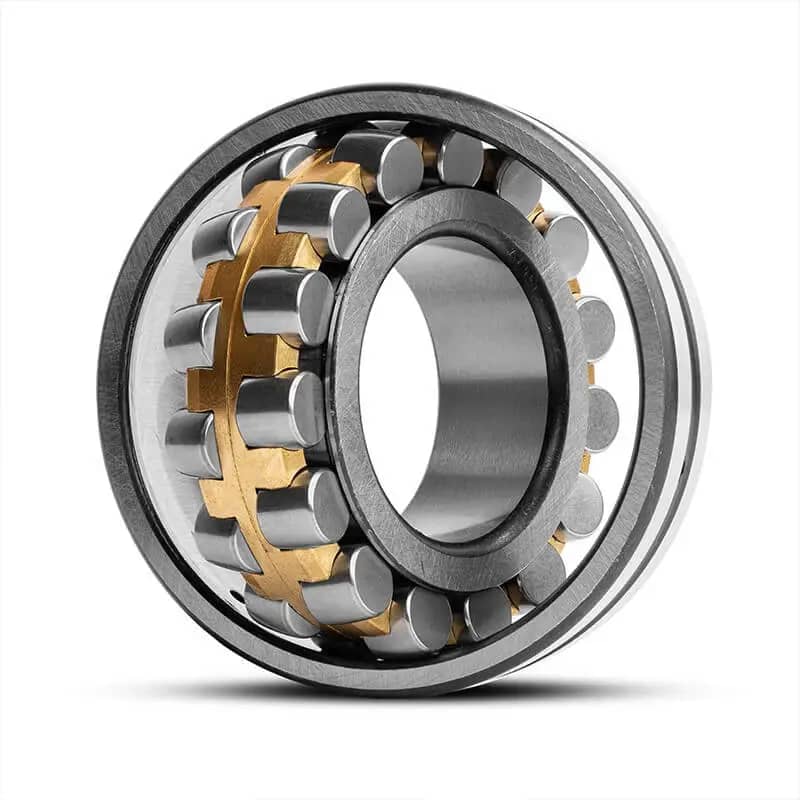
Usage and Applications: Roller Bearings are known for their robustness and are primarily used where high load capacity is required. They come in various types including cylindrical, tapered, spherical, and needle bearings, each suited to specific applications such as:
- Automotive wheels
- Industrial gearboxes
- Wind turbines
- Mining and construction equipment
Benefits of Roller Bearings
Versatility: Available in various shapes and sizes, catering to a wide range of industrial needs.
Load Capacity: Especially high radial load capacity, suitable for heavy-duty applications.
Durability: Tends to have a longer operational life under heavy-load conditions.
Here’s a table summarizing the usage, applications, and benefits of Angular Contact Ball Bearings and Roller Bearings:
Bearing Type | Usage | Applications | Benefits |
---|---|---|---|
Angular Contact Ball Bearings | High-speed and precision operations | High-speed spindles, precision milling machines, gearboxes, pumps | High load capacity, precision, operates well at high speeds |
Roller Bearings | High load capacities, robust applications | Automotive wheels, industrial gearboxes, wind turbines, construction | Versatile, high radial load capacity, durable |
Key Differences between Angular Contact Ball Bearings and Roller Bearings
Load Handling: Roller bearings generally handle higher radial loads, making them suitable for heavy-duty applications. In contrast, angular contact ball bearings are better suited for applications requiring precision under combined radial and axial loads.
Speed Capability: Angular contact ball bearings are typically better suited for high-speed applications due to their ability to minimize friction and heat build-up.
Applications: The choice between these two types of bearings largely depends on the specific load and speed requirements of the application. Angular contact bearings are preferable in high-speed, precision applications, while roller bearings are ideal for high-load, high-durability applications.
Here’s a table summarizing the differences between Angular Contact Ball Bearings and Roller Bearings:
Angular Contact Ball Bearings | Roller Bearings |
---|---|
Better suited for high-speed applications | Generally, handle higher radial loads |
Designed for high precision under combined loads | More suitable for heavy-duty applications |
Capable of operating with minimal friction | Have a longer operational life under heavy loads |
Ideal for precision applications such as spindles | Commonly used in heavy machinery like mining equipment |
Choosing the Right Bearings for your Needs
Deciding between angular contact ball bearings and roller bearings involves considering the operational conditions of your machinery. If your primary concern is high precision and high-speed operation, angular contact ball bearings are likely the better choice. However, for applications that involve heavy loads and require robust durability, roller bearings will generally be more suitable.
Conclusion
Both Angular Contact Ball Bearings and Roller Bearings have their unique strengths and ideal applications. By understanding the specific needs of your machinery, you can make an informed decision that enhances performance and extends the lifespan of your equipment.
For businesses looking to source premium bearings that maximize efficiency and reliability, KG International stands ready to meet your needs. Whether you are gearing up for a new project or upgrading existing machinery, contact KG International today to explore high-quality bearings solutions. Visit KG International for more information and to discuss your project requirements with experts now.